We're taking shiplifts and shipyards to new heights by asking the right questions
Need to increase your shipyard’s drydocking capacity but not sure where to start? Taking the time to understand six core considerations at the very beginning of shiplift drydock design will save you time and money and avoid costly mistakes. We’ll take that time with you to arrive at a winning game plan that fits your yard’s distinct set of variables.
If it's in a drydock, it's not in the water serving its mission.
Speed. Efficiency. Operational Availability. No more waiting for one vessel to complete repairs before starting a second – the OmniLift and transfer system will move as many vessels as there are working bays. No more waiting to drain and fill the graving dock – the OmniLift is always ready to lift and lower vessels out and into the water.
Reignite Your Yard and Shiplift Potential
Six core factors to understand
Read nowRead Robert Taylor’s paper, “Improving Multi-Use Port Facilities through Key Design Parameters”, presented at the 35th PIANC World Congress in South Africa.
Geology
Controlling overall project costs begins with understanding local geology. Geology governs dredging costs, soil retention methodology, foundation system type, and capacity. Understanding the geology, configuring the system to optimize the civil foundation system capacity, and controlling dredging costs are key to achieving the lowest possible installed facility cost.
Geometry
Is this a new yard with more flexibility in building layout, or are there existing constraints when maneuvering ships to the work areas? Perhaps the channel access has features that affect the layout.
Operational Objectives
Refit, inspection, or new builds? Maybe all of the above. Will your region be experiencing an increase in demand to maintain vessels related to offshore wind? How about modifications to propulsion and emissions treatment systems needed to meet new regulatory and sustainability requirements for vessels operating in your region?
Target Market
What types of ships is this shiplift intended to lift? We’ll help you define you’re target market and find the perfect shiplift size with Bardex’s Predictive Intelligence.
Engineering, Procurement, Construction (EPC) Plan
What resources are available in your region to support the implementation and future operations of your project?
Financial Plan
You know you need more capacity, but how do you prepare to present the best business case to management? Bardex will assist you with data analytics that provide insight into the regional demand for service.
Elevate your yard
Our chain jack shiplift technology is the gold standard in accuracy, reliability, and sustained value over the 40+ year service life you can expect from your investment. Why?
Fewer Moving Parts → Less Maintenance → Less Downtime → More Revenue & Less Hassle. Win-Win.
Maintenance-prone items, such as variable frequency drives (VFDs) susceptible to overheating, gearboxes, brakes, bearings, sheaves, and wire ropes, are nowhere to be found in our shiplift designs. Neither is environmental pollution caused by submerging greased wire ropes and sheaves. And our chain based system will never experience a failure resulting from a rope skipping a sheave, snagging, and breaking due to debris lodged in the submerged lower sheaves. This risk is unique to operating a wire rope shiplift block underwater that does not normally occur with other similar types of marine or land based wire rope lifting equipment. Modern-day genius at its simple best.
Meeting official standards, exceeding your expectations
Our shiplifts meet (and in some cases exceed) the common standards below, and we would be happy to discuss any not listed here.
- Lloyd’s Code for Lifting Appliances in a Marine Environment for classification or certification
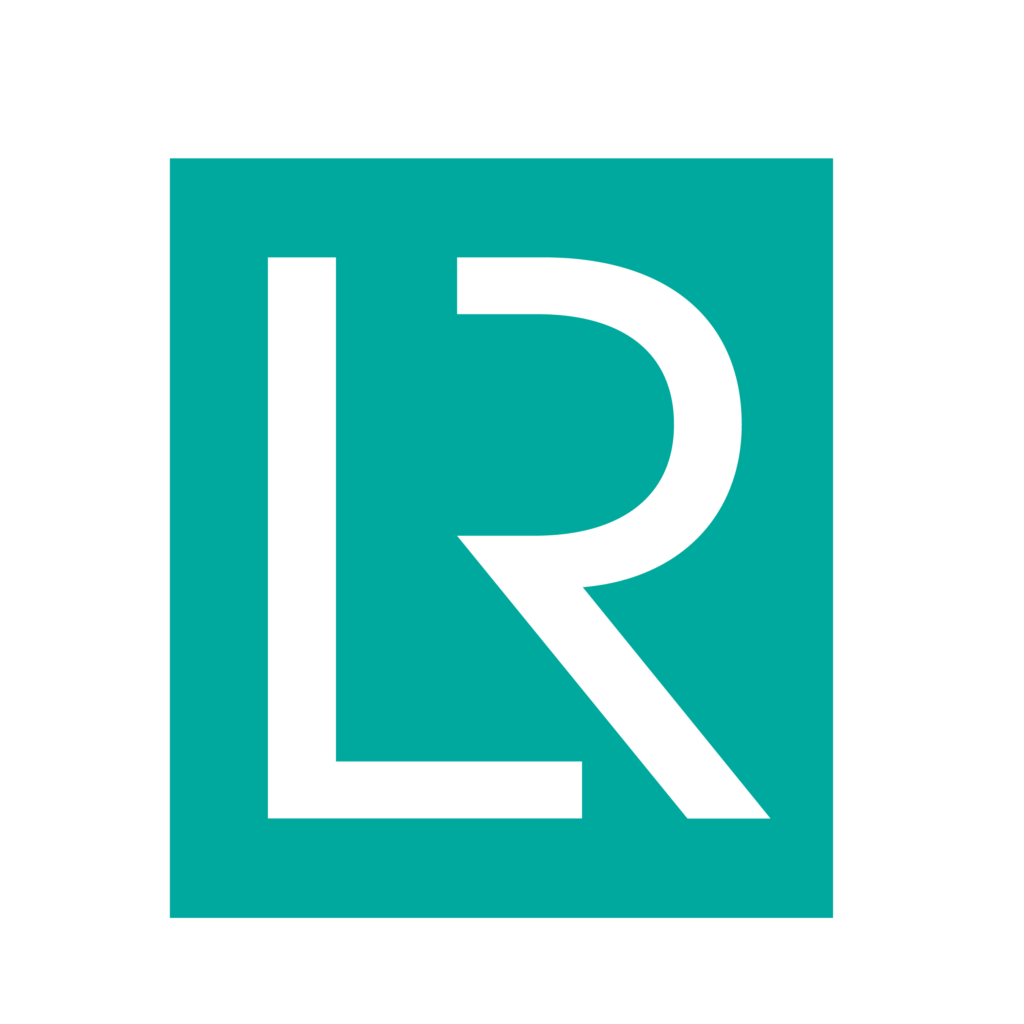
- NAVSEA’s Safety Certification Program for Drydocking Facilities and Shipbuilding Ways for U.S. Navy Ships (MIL-STD-1625D(SH)
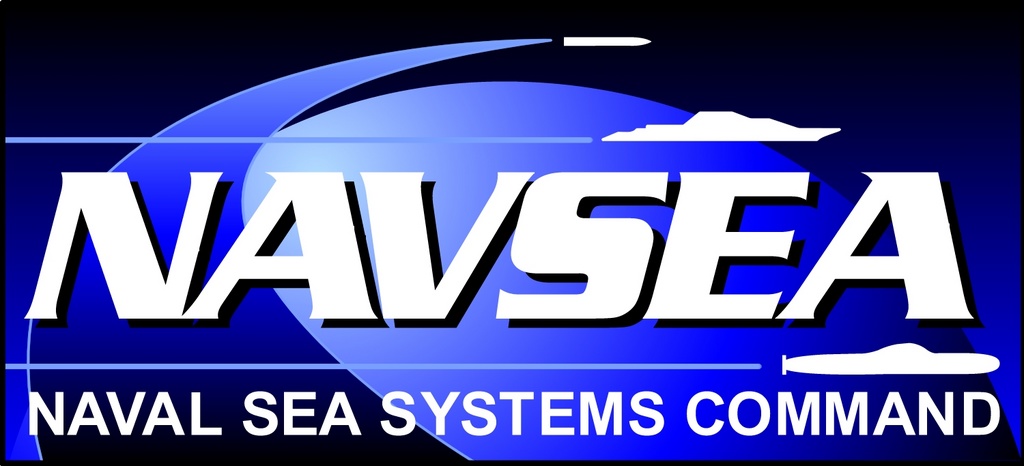
- The Coast Guard’s Surface Forces Logistics Center’s (SFLC) Standard Specification 8634 – Drydocking
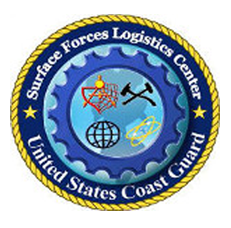
- DNV-GL’s DNV-ST-0377, “Shipboard Lifting Appliances”
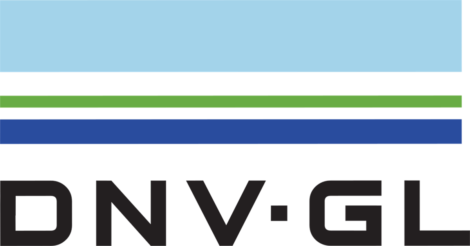
The best teams work together. Shouldn’t each of your lift stations work in sync too?
Accurate position control and synchronization provide a perfectly level lift down to 1mm across the entire platform without operator intervention.
Is Your Legacy Wire Rope Shiplift System Driving Costs Up?
What goes up must come down, and Bardex will work with you to forge a path forward.
What does that path forward look like?
- Using the existing civil works with little to no modifications
- Reducing the quantity and size of piles under the shiplift piers by up to 33%
- Reducing concrete for pier construction by up to 50%
- Reducing pile cap thickness by up to 25%
- Increasing your market share and revenue potential resulting from up to 25% more lift capacity with the same number of lift stations
- 20% to 33% reduction in operating expenses vs legacy wire rope systems
- Upgradeable after original duty life or when your yard outgrows its current needs, as some of our repeat customers have
Making the switch from wire rope to chain jacks is simple.
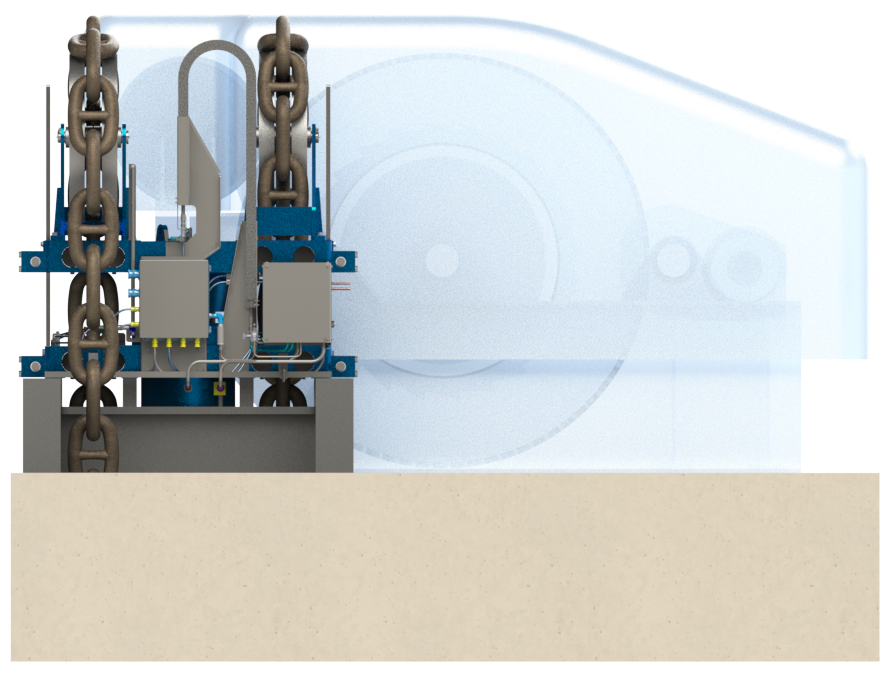
The chain jack occupies only one-third the space of a winch in wire rope systems.
Optimize by Using All Available Yard Space with A Transfer System
How do you move a vessel from an OmniDock to land? With a transfer system of course!
A Chain Jack? What’s that?
The gold standard for shiplift technology
One of Bardex’s most important product innovations and contributions to the heavy load handling industry is the Linear Chain Jack. This piece of equipment represents one of the safest and most efficient ways to lift, tension, or move heavy loads using chain.
Unlike a wire rope drum with fleet angles, and as the word “Linear” in the product’s name implies, the chain is always lifted, pulled, or tensioned in a straight line. There are no induced link bending stresses or interlink wear from bending it around a chainwheel under load.
The Bardex Linear Chain Jack has a significantly reduced footprint compared with windlasses, winches, and other devices.
Bardex has designed the Linear Chain Jack so that the chain is always mechanically held by either the fixed or traveling latches. This makes it impossible for the chain to be released inadvertently due to loss of hydraulic power or operator error.