Operational Excellence Starts with Informed Decisions
Having the right tool for the job makes all the difference. We’ve engineered the OmniLift™ line of shiplifts to deliver superior performance, safety, and durability. This side-by-side comparison highlights how our product outperforms the competition—offering greater long-term value, seamless integration, and the resilience to excel in even the harshest conditions. See what information has guided leaders to the only vessel sustainment solution that rises to every challenge.
OmniLift™: Shiplift by Bardex
Facility Space
- Small footprint, requiring only one-third the space of a winch
- Scalable technology provides the same lifting capacity with fewer lift stations, as well as lower up-front and maintenance costs throughout the life of the system
- Narrower pier widths and fewer piles reduce civil costs
Wire Rope Winch Shiplift
Facility Space
- Takes up 66% more space than a chain lift
- Larger pier widths and more piles than with chain
OmniLift™: Shiplift by Bardex
Usability
- Simple components, consisting of a single lift cylinder and two small latch actuators controlled by an off-the-shelf control valve
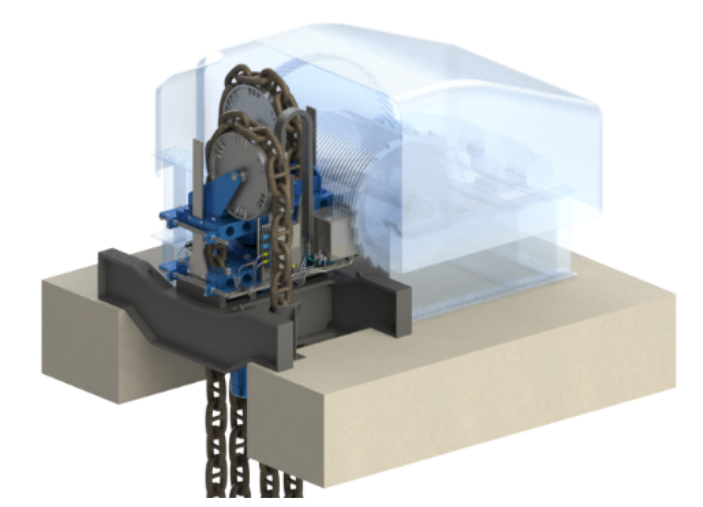
- Straight-line lifting: No highly loaded winch drums or sheaves and no bending loaded lift element, as there is with wire rope
- Superior corrosion resistance and easy inspection
- Increased safety: Two chains at each lift station for a redundant lifting design
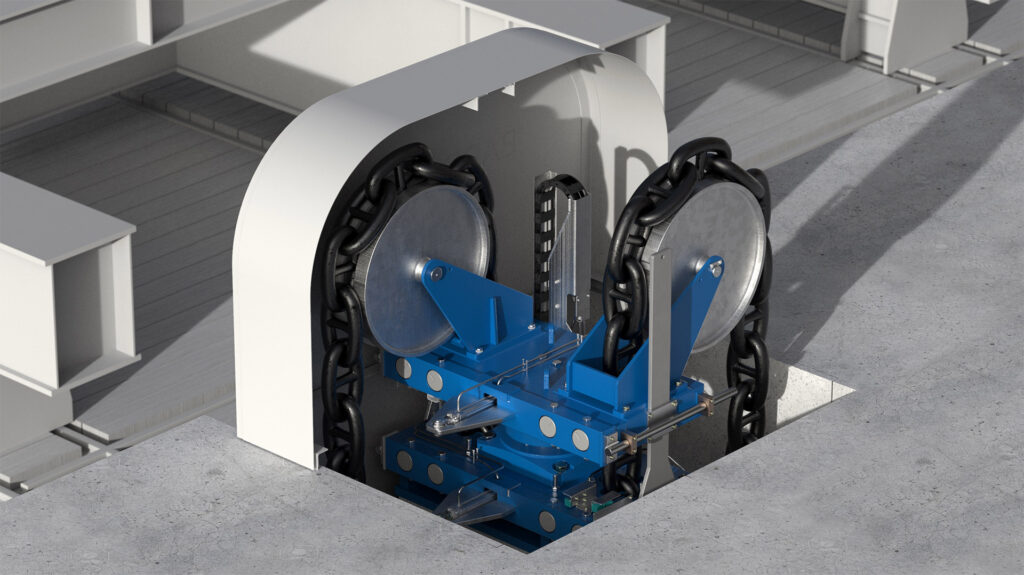
- Each chain is designed for the full capacity, with a 1.5:1 safety factor per chain, or a total safety factor of 3:1 with two chains
- Chains under load do not wrap around a sheave or drum and, thus, do not incur the wear and fatigue associated with wire-rope storage
- No spiral strands twisting under load
Wire Rope
Usability
- Corrodes from the inside out, requiring destructive testing or expensive inspection equipment
- Wire rope is sized for 12.5% of the winch load, not the full load

- If any part of the 8-part line fails, the whole system fails
- Known wire rope failures occur at an approximate rate of one per year globally, with at least one incident occurring during final testing of a new system
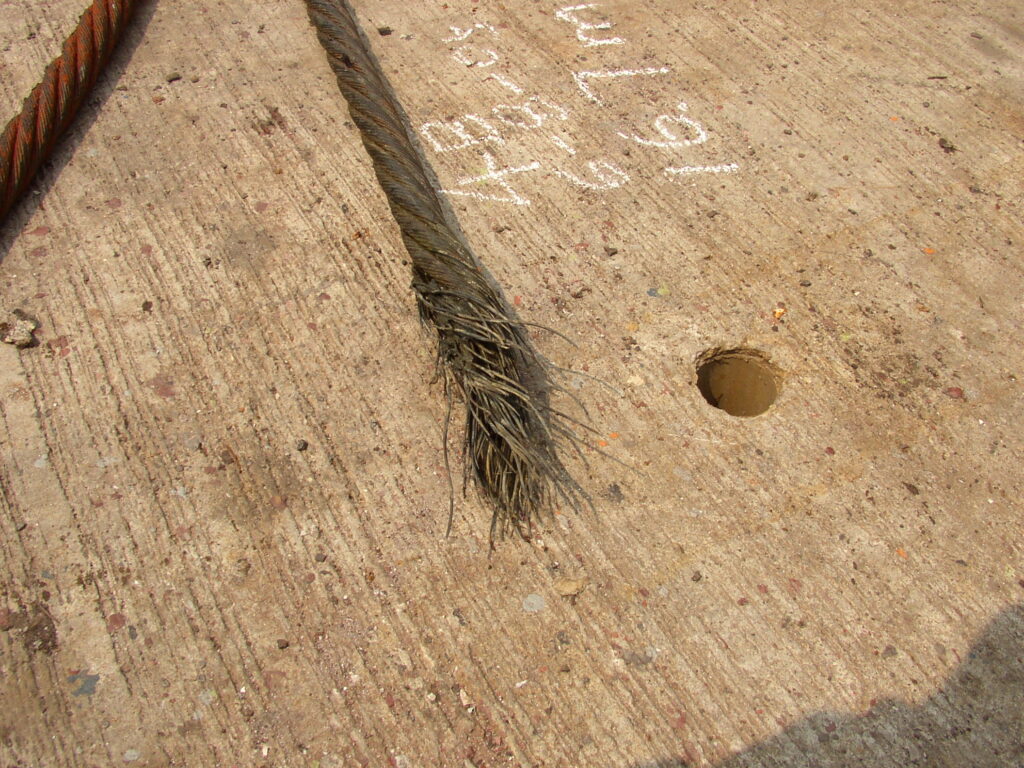
- Wire ropes stretch 15x more than chains
- Typical cranes using wire ropes do not submerge the wire ropes in seawater; comparing that use case with wire rope shiplifts is like comparing apples and oranges
- Winches used with wire ropes have poor load-monitoring accuracy due to their many wraps around sheaves, wire rope fleet angle, and bearing friction; aggregate error is over 15%
- Wire rope systems have no redundancy
OmniLift™: Shiplift by Bardex
Parts & Maintenance
- Chain jacks do not use pulley sheaves
- Simple maintenance
- Bardex offers options to stock spare parts in or near your facility; most parts are also readily available from local suppliers
Wire Rope
Parts & Maintenance
- Wire ropes can corrode from the inside, avoiding detection, and need to be replaced every 5 years
- High maintenance components: gearboxes, wire ropes from limited manufacturers, brakes, and electronic drives.
- Platform-mounted sheaves, subject to the full load of the winch, are submerged in seawater every time the platform is lowered
- Bearings are submerged with each operation and need to be replaced every 2 years
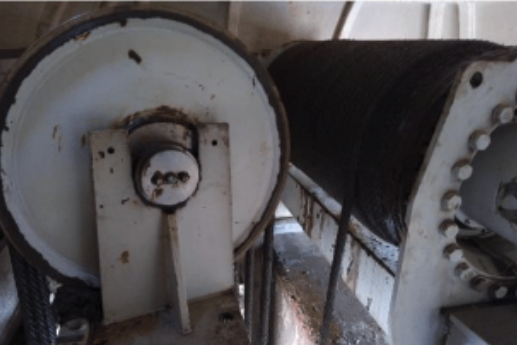
OmniLift™: Shiplift by Bardex
Lloyd’s Code Inspection
Connection to Platform
- No Lloyd’s inspection required
Chain Jack
- No Lloyd’s inspection required
Insulation Resistance
- No Lloyd’s inspection required
Chain Maintenance and Inspection
- Any length of chain so worn that its mean diameter at its most worn part is reduced by 4% or more from its nominal diameter is to be renewed. This is an easy visual inspection/measurement with no need to do any disassembly.
Wire Rope
Lloyd’s Code Inspection
Connection to Platform
- Must conduct inspections at all levels
- 20% of all sheaves, bearings, axles, and housings are to be examined yearly, with at least two complete sets of sheaves disassembled for examination
- All sheaves are to be disassembled at least once in the 5-yearly survey cycle
Wire Rope Hoist – Annual Periodical Surveys
- Tooth alignment for gears
- Main shaft pillow block bearings opened
- Re-torque screws securing final spur wheels to the drum
- Primary gears, shafts, and bearings
- Hoist frame and bolting
Electrical Systems Test
- Electric motor insulation resistance test
- Breakers, relays, and all mechanical electrical gear examined
- 20% of electric motors including bearings and magnetic brakes examined
- All circuit breakers tested for overload tripping
- Air compressors for hoist ratchet and air tank examined
- Demonstration of all safety devices
Rope Maintenance and Inspection
- Annual visual examination for signs of corrosion, wear, or broken wires
- Wire ropes are to be renewed when 5% or more of wires in any length of 10 rope diameters is broken, worn, or corroded; for small installations, this will result in a replacement cycle of about 5 years
OmniLift™: Shiplift by Bardex
Longevity
- Two 4-person crews can replace 92 chains in one week (46 chain jacks with two chains each); replaced every 12-15 years
- 5 days x 8 persons = 40 person-days over 24 to 30 years
- The fatigue life of chains far exceeds their duty life in this application, so is not a concern
Wire Rope
Longevity
- Crew of 4 for 3-5 days to replace two wire ropes; for a 46-hoist system, 10 ropes must be replaced annually
- 5 days x 4 persons x 5 rope pairs = 100 person-days = 3000 person-days over 30 years
OmniLift™: Shiplift by Bardex
Environmental Considerations
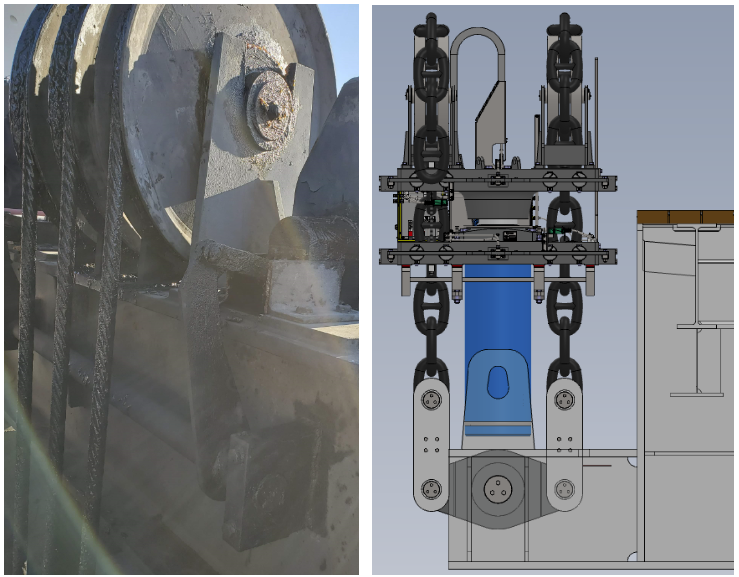
- Chain jack systems do not submerge any greased or lubricated parts
- Extreme measures are taken to ensure no leaks of hydraulic fluid, which is also readily biodegradable for added environmental safety
- Drip trays and curbs offer further protection from accidental spills
- Carefully selected safety factors provide a high level of security against component failure
Wire Rope
Environmental Considerations
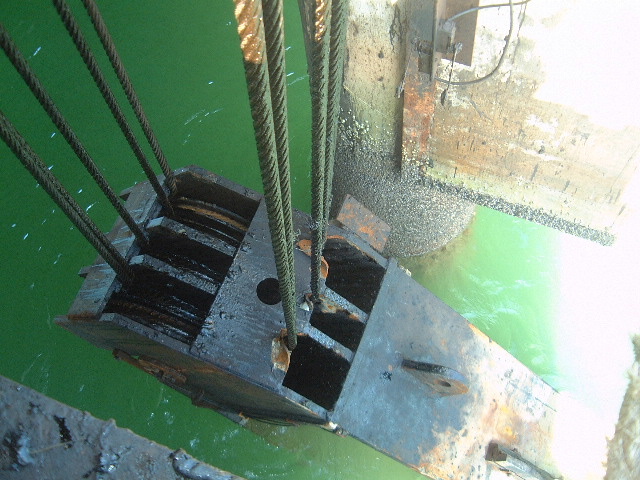
- Deliberately submerge heavily greased rope and pulley sheaves into the water with every operation
- Grease must be re-applied once per month at a minimum
- Grease is not allowed in some jurisdictions
OmniLift™: Shiplift by Bardex
Operation
- PLC controlled for automatic operation
- Adjustable lift/lower speed depending on vessel weight equal to speeds of wire rope systems
- No active adjustments needed for vessel transfer on and off the shiplift platform
- Weight-distribution measurement capability
- Ultra-precise synchronization: A level platform is achieved after every stroke; lift cylinders are synchronized within +/-1mm throughout cycle
- Mechanically locked at all times: No positional adjustments for transfer required
- No operating depth limit because chain does not require storage drums
- Smooth and quiet operation: No sudden movements or shock loading
Wire Rope
Operation
- Annual removal and destructive test of a minimum of 2 ropes; more ropes required if wire breaks at less than 90% MBL
- It is the intention that all ropes be replaced in sequence at a rate determined by wear, chemical attack, corrosion, or other forms of deterioration associated with the particular installation